The Any-Job, Any-Industry Laser Partner
Laser welding at Applied Fusion
In the late 70s, we pioneered laser applications and integrated them into the job shop environment, which opened up possibilities that were once not achievable with conventional methods. Today, it’s a common occurrence to have customers schedule time in our laser lab and work directly with our staff to establish parameter settings and techniques before designs are finalized. If you’d like to schedule time in our laser lab as well, contact us.
Our laser welding team works closely with different industries such as medical, aerospace, automotive, semiconductor and defense. Our willingness to tackle any job helped establish us as a friendly, competent, service-oriented laser job shop. We also provide metallography services by cross-sectioning and photographing welds, documenting and establishing process qualification reports and other necessary data. We can assist with material selection, metallurgy issues, joint designs and stress analysis.
If tooling or fixturing is required, our in-house machine shop is also available. Our qualified staff has the ability to design and fabricate tooling to assist your laser project within one day’s time. In fact, we can easily provide a full turnkey service by manufacturing your products complete if you so desire, saving time and money in most cases.
When to opt for laser welding
Generally, LASER welding is a great option when it’s necessary to weld thin material (.001 thick foils to .060 thick) when conventional or electron beam welding is not practical. One main advantage is that the workpiece can be handled and fixtured in atmosphere, minimizing tooling and complex fixturing. The operator can handle the parts easily and, in some cases, the welds are performed under a microscope for visual assistance on small components and micro welds.
Another major advantage of a LASER weld is that the heat input is extremely focused and direct. The heat affected zone (HAZ) is the most narrow of any form of welding. This also allows us to place welds close to critical areas that may have a coating or sensitive electronic nearby. The heat is so minimal that you could touch the weld zone seconds after without getting burned. In many cases, parts can be completely finish-machined and then final welded without having to perform any post-weld machining because the warpage is so minimal. The welds have a nice cosmetic appearance as well.
What we laser weld at Applied Fusion
We typically weld bellows, apertures, thermocouple wires, various designs of water and gas covers and a large variety of feedthrus. Components that have magnets are also easily welded because the LASER is not affected by magnetic fields the way the electron beam is. Much of our work involves high vacuum apparatus, and the LASER weld is an excellent choice for penetration requirements that do not exceed .060. Our helium mass spectrometer vacuum leak detectors are on standby to certify sound and vacuum tight welds.
Cutting and drilling are also commonplace for thin material (.001 thick to .100 thick) where conventional machining is not possible or practical. Our LASERs can drill holes as small as .001 diameter depending on the thickness.
We have the privilege of working with engineers who are developing cutting edge technologies. Our highly skilled operators on the laser welding team enjoy the challenges and demands that our customers bring on a consistent basis. We treat them as partners by sharing our expertise and providing them professional and quick service. This saves our customers time and money while ensuring positive and rapid results. Applied Fusion’s LASER team is dedicated to customer satisfaction.
Our laser welding equipment
We have 4-axis CNC CO2 and Nd YAG LASER machines to assist you with your welding, cutting and drilling needs. The CO2 Lasers are commonly used on stainless steel alloys, titanium, nickel, wood and plastics while the YAG is more suitable to aluminum, precious metals, copper, tantalum and molybdenum.
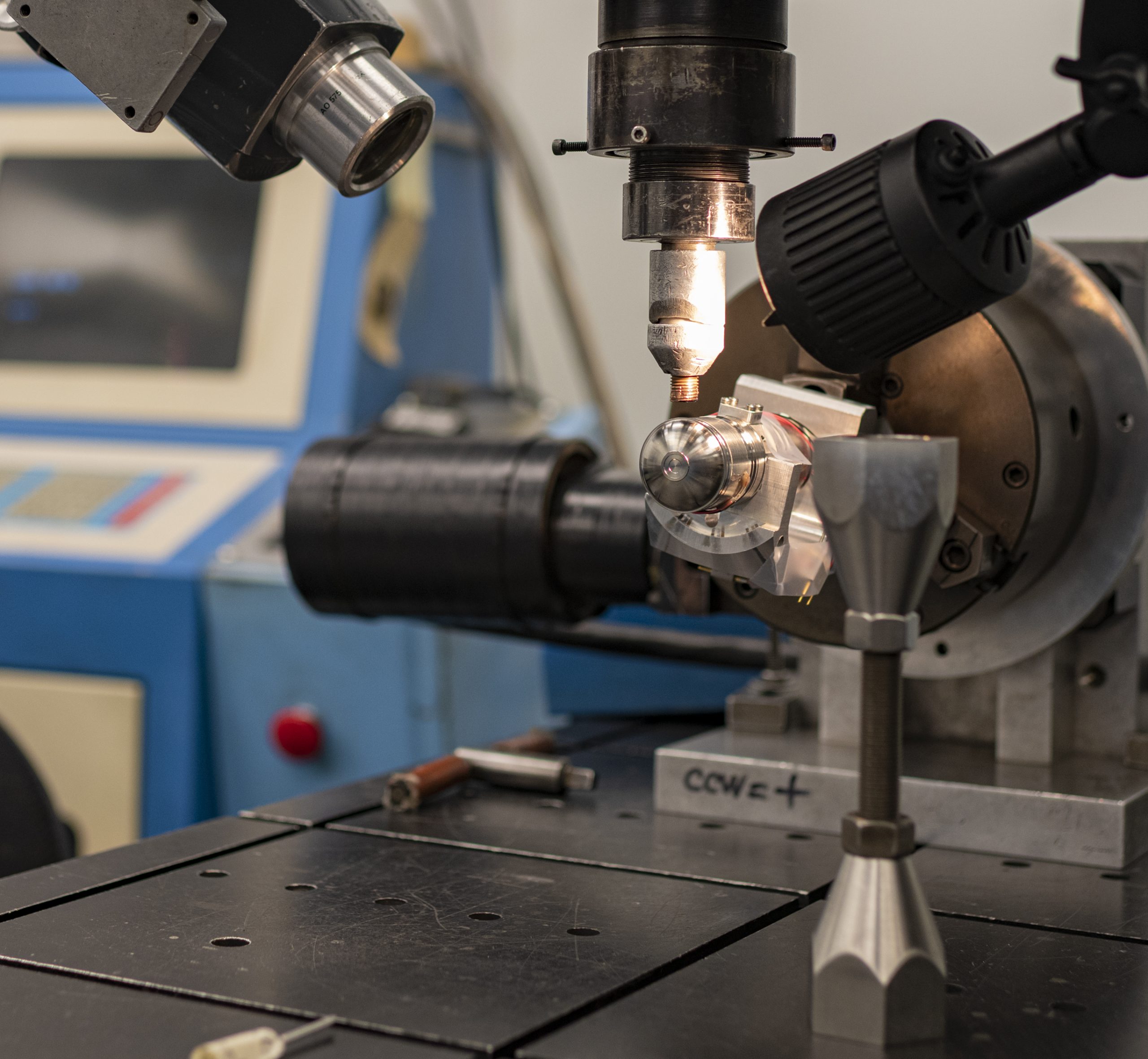
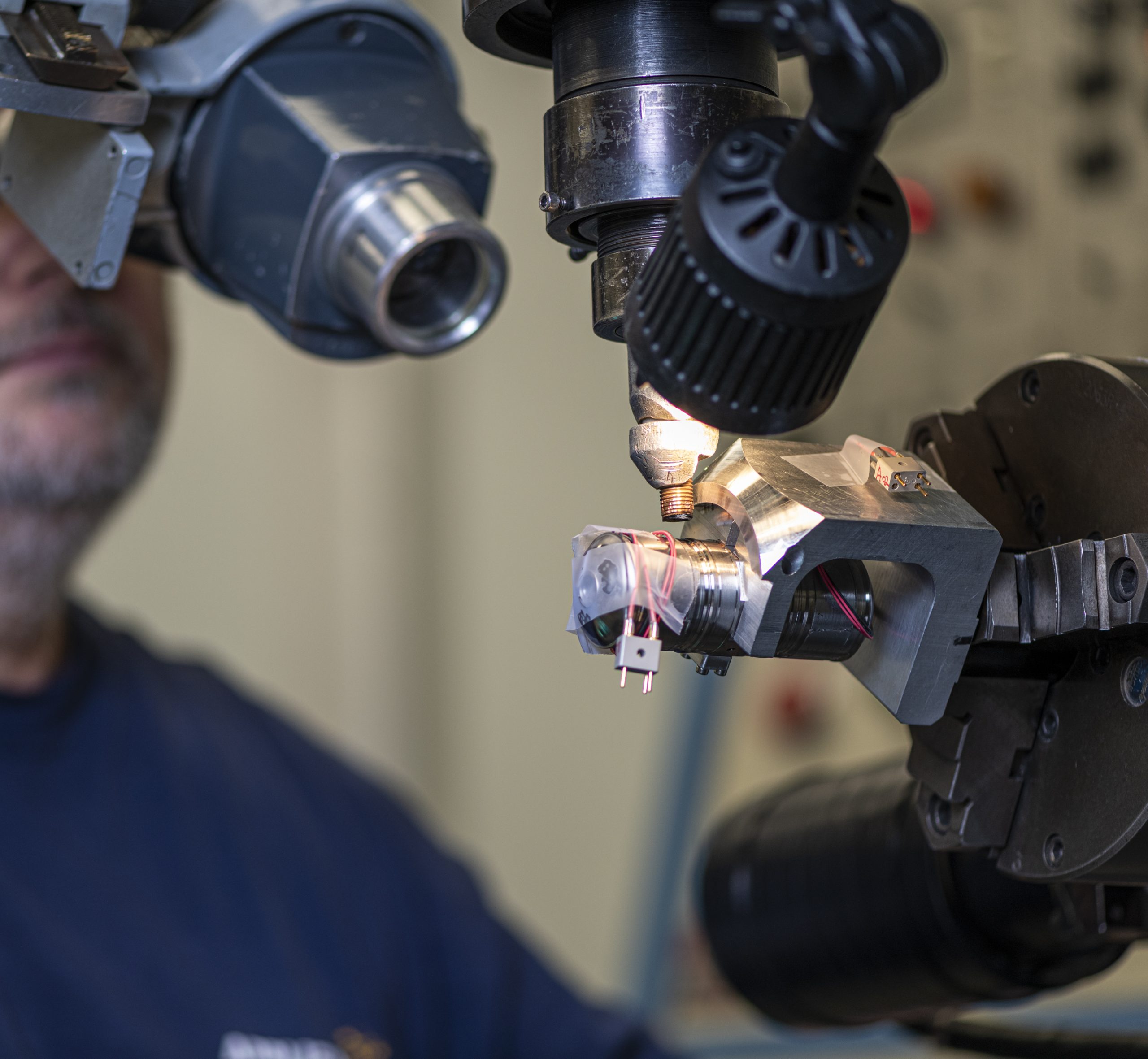
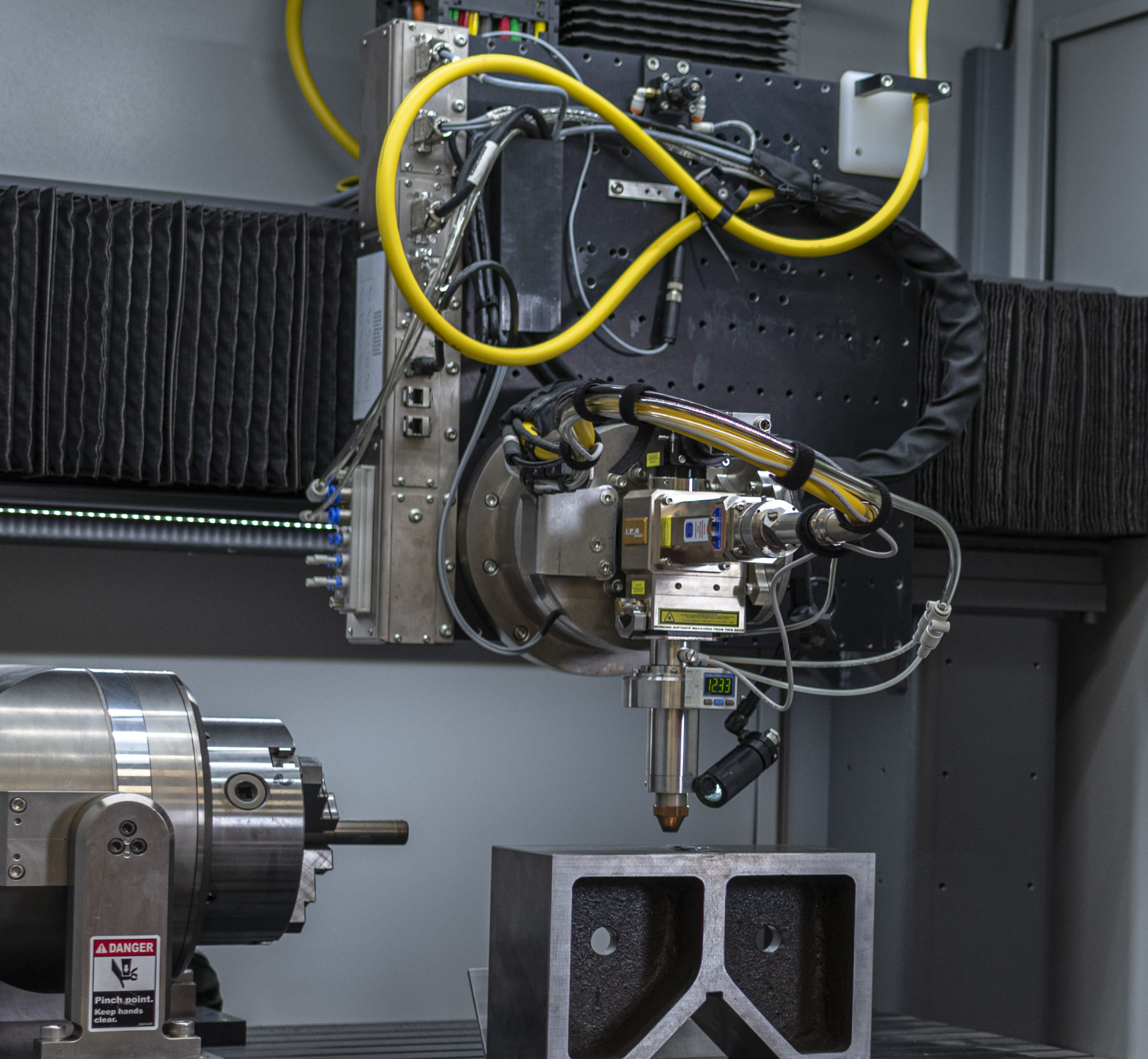
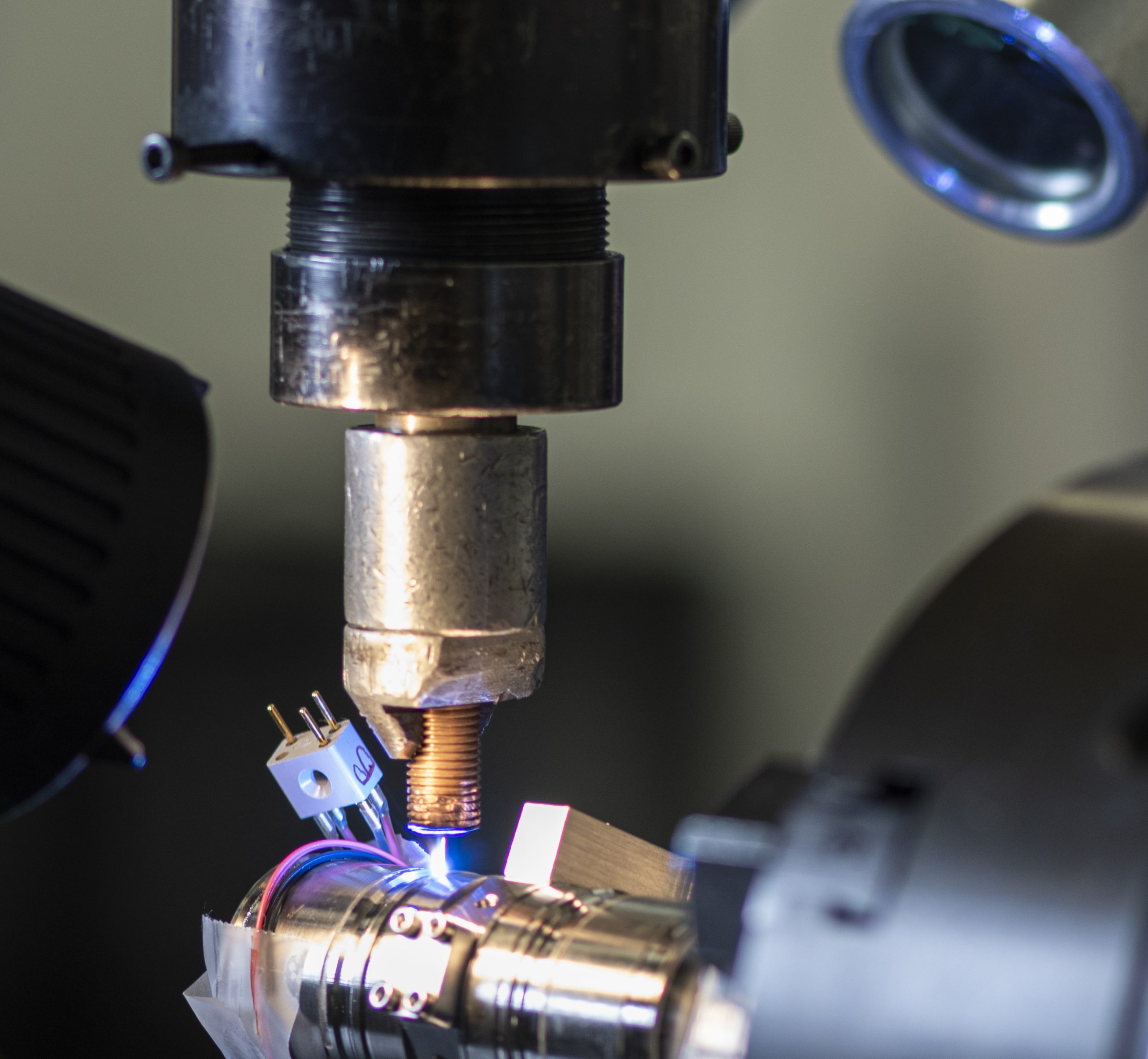